Understanding the Refrigerant Transition
Understanding the Refrigerant Transition: What Facility Managers Need to Know
In the realm of HVAC systems, one of the most pressing topics today is the transition of refrigerants. This shift is driven by the imperative to mitigate global warming potential (GWP) and align with decarbonization efforts. In a recent webinar hosted by Trane, industry experts delved into the reasons behind this transition and what it means for facility managers of national retail chains, some of whom may have varying levels of familiarity with HVAC technologies.
Why the Change?
Historically, concerns over ozone depletion spurred regulatory actions that have successfully mitigated these issues by 2040. Today, the focus has shifted to combatting global warming, with refrigerants identified as significant contributors to environmental impact. The new refrigerants, such as R-454B and R-32, aim to significantly reduce GWP compared to the current industry standard, R-410A.
Key Transition Milestones
The transition timeline outlines gradual reductions in GWP targets, starting with a 40% reduction by 2025 and further reductions by 2029. These efforts are part of a broader strategy to enhance environmental sustainability within the HVAC industry.
Comparison of New Refrigerants
The industry has narrowed down the choices to two main alternatives: R-454B and R-32. Both options exhibit low toxicity and are relatively efficient, but their critical distinction lies in their GWP, which is substantially lower than that of R-410A. While R-454B offers a longer-term solution with a GWP that supports operational use until 2035, R-32 presents a viable option for specific applications within current equipment frameworks.
Flammability and Safety
One of the primary concerns voiced during the webinar was the flammability of the new refrigerants. While both R-454B and R-32 are classified as mildly flammable (A2L), experts reassured attendees that these refrigerants pose minimal risk under normal operating conditions. Safety measures, including specialized sensors, are being integrated into new equipment to detect and mitigate potential leaks swiftly.
Implementation and Considerations for Facility Managers
Effective January 1, 2025, manufacturers will cease producing R-410A systems in the U.S., shifting production exclusively to R-454B and R-32. Existing R-410A equipment inventory can continue to be sold by manufacturers until 2028. R-410A systems will continue to work after the phase out but the costs associated with repair may increase.
Cost and Viability
Concerns were raised about the cost implications of transitioning to new refrigerants. Historically, as seen with previous transitions, initial costs for new refrigerants may be higher due to limited supply and increased demand. However, over time, as production scales and technologies mature, costs are expected to stabilize and potentially decrease.
Future Outlook and Adaptation
Looking ahead, ongoing research and development aim to address challenges such as finding viable drop-in replacements for legacy systems and optimizing the efficiency of new refrigerants. Facility managers are encouraged to stay informed about evolving regulations and technological advancements to make informed decisions regarding their HVAC systems.
In conclusion, while the refrigerant transition presents significant challenges and considerations for facility managers, it also represents a critical step towards environmental stewardship and sustainability within the HVAC industry. By understanding the implications and planning proactively, facility managers can navigate this transition effectively, ensuring compliance and optimizing system performance for years to come.
Stay compliant and ahead of the curve! Our 1-page cheat sheet provides you with all the key dates, rules, and refrigerant details. Get your free copy today by clicking here!
For even more information on the U.S. Environmental Protection Agency’s (EPA) refrigerant regulations, read their Final Rule Sheet available at: https://www.epa.gov/system/files/documents/2023-10/technology-transitions-final-rule-fact-sheet-2023.pdf
How is your facility preparing for the refrigerant transition? Are you facing challenges or already making changes? Share your thoughts in the comments—we’d love to hear from you!

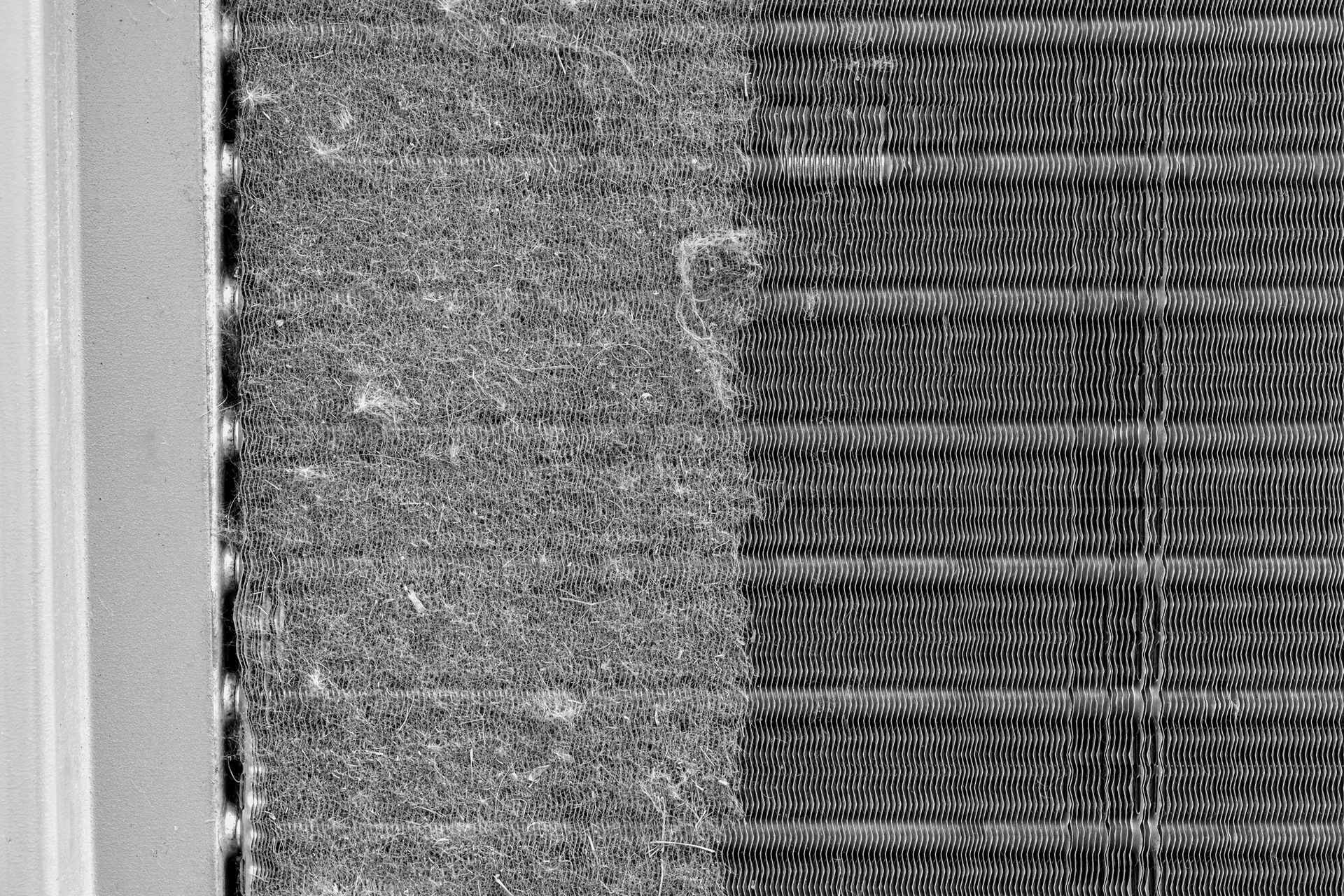
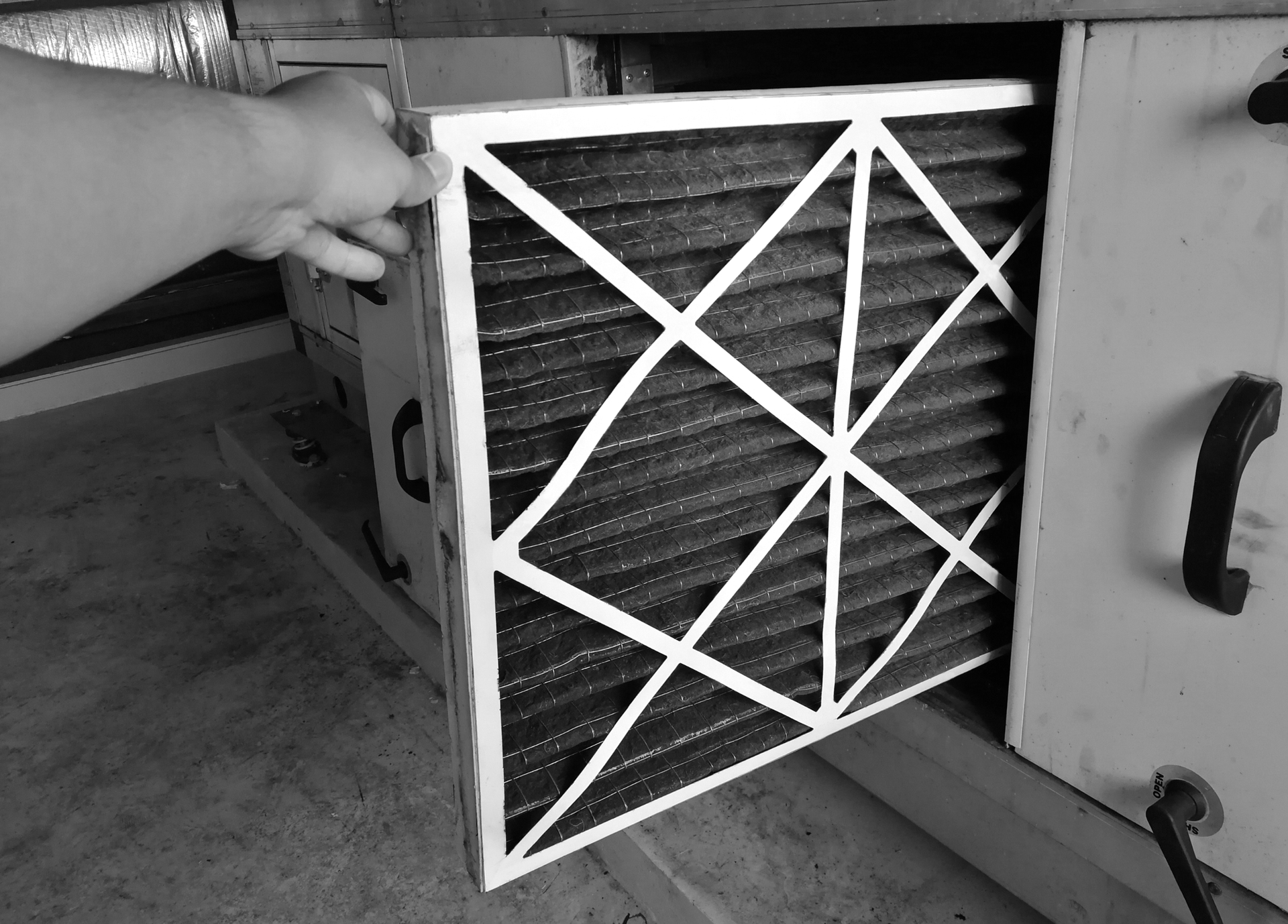