PM or Pay More
PM or Pay More:
Why PMs Are a Must for Your Business
For commercial facility managers overseeing HVAC systems across a chain of retail stores, restaurants, banks, healthcare facilities, storage facilities, and other national commercial locations, Preventative Maintenance (PM) is a critical, yet often overlooked, aspect of building operations. Understanding the fundamentals of HVAC maintenance and the direct impact it has on your business can mean the difference between smooth operations and costly disruptions.
Why Preventative Maintenance is Essential
HVAC systems are the backbone of a commercial property, ensuring a comfortable environment for customers, employees, and sensitive equipment while preserving the integrity of perishable goods and maintaining regulatory compliance. Unlike reactive maintenance, where issues are addressed only after a failure, preventative maintenance is a proactive approach designed to keep HVAC equipment running efficiently, reducing the likelihood of unexpected breakdowns.
The Impact on Commercial Chains
For businesses that operate multiple locations, a well-maintained HVAC system is a necessity. Consider the following:
- Customer Experience: In retail and banking, a location that’s too hot or too cold can drive customers away, reducing sales and negatively impacting brand perception.
- Employee Productivity: Employees struggling in an uncomfortable environment are less productive, leading to decreased efficiency and higher turnover.
- Product & Equipment Protection: Restaurants and grocery stores rely on climate control to maintain food safety standards, while many retail stores require temperature stability for inventory like cosmetics, electronics, or pharmaceuticals. Storage facilities depend on precise climate control to prevent damage to stored goods, and healthcare facilities must maintain strict temperature regulations for patient comfort and medical equipment.
- Regulatory Compliance: Healthcare facilities and pharmacies must adhere to stringent HVAC standards, including ASHRAE and CDC guidelines, to ensure patient safety and prevent the spread of airborne contaminants.
What Happens Without Preventative Maintenance?
Ignoring preventative maintenance can lead to significant operational challenges, including:
- Increased Downtime: HVAC system failures often happen at the worst possible time—on the hottest or coldest days of the year when the system is working its hardest. Unplanned downtime can force store closures, halt bank operations, or even put patient safety at risk in healthcare settings.
- Higher Repair Costs: Minor issues that go unchecked can snowball into major component failures, resulting in expensive emergency repairs or complete system replacements.
- Reduced Equipment Lifespan: HVAC systems that don’t receive regular maintenance accumulate wear and tear at an accelerated rate, forcing earlier-than-expected capital expenditures.
- Energy Inefficiency: According to the U.S. Department of Energy, HVAC systems account for approximately 40% of a commercial building’s energy consumption. A neglected system works harder to maintain temperature, consuming more energy and inflating utility bills.
Key Preventative Maintenance Practices
Preventative maintenance should be performed on a scheduled basis, with key tasks including:
- Filter Replacements: Dirty filters restrict airflow, reducing efficiency and increasing strain on the system. The Department of Energy states that replacing clogged filters can lower HVAC energy consumption by up to 15%.
- Coil Cleaning: Evaporator and condenser coils accumulate dirt and debris over time, decreasing efficiency and leading to overheating or freezing.
- Drain Line Checks: Blocked condensate drain lines can lead to water damage and mold growth, creating additional maintenance headaches.
- Belt & Motor Inspections: Worn belts and malfunctioning motors can cause system inefficiencies and premature component failure.
- Refrigerant Level Checks: Low refrigerant levels indicate leaks or system inefficiencies that need to be addressed to prevent costly breakdowns.
- Smart Monitoring Solutions: Many commercial chains are turning to IoT-based monitoring systems that provide real-time data on HVAC performance, helping facility managers anticipate and address maintenance needs before failures occur.
Financial Implications of Inconsistent PM
When budgeting for maintenance, it’s important to recognize that preventative maintenance is not just an expense—it’s an investment. Studies by the Building Owners and Managers Association (BOMA) indicate that every $1 spent on PM can save $4–$5 in repair and energy costs. Additionally, a proactive maintenance program helps avoid:
- Emergency repair premiums – Last-minute service calls are significantly more expensive than scheduled maintenance visits.
- Lost revenue due to downtime – A closed store, bank, or healthcare facility due to HVAC failure can result in thousands of dollars in lost sales or, in the case of healthcare, serious patient safety risks.
- Early equipment replacement costs – A well-maintained system lasts significantly longer than a neglected one.
Conclusion HVAC preventative maintenance is a critical practice for commercial facility managers overseeing multiple locations. By implementing a proactive PM program, businesses can extend the life of their equipment, reduce operational costs, and ensure a comfortable environment for customers and employees. Investing in routine maintenance today can save thousands in emergency repairs, energy costs, and lost revenue tomorrow. For those managing retail chains, restaurants, banks, healthcare facilities, storage units, or other commercial properties, making preventative HVAC maintenance a priority isn’t just about maintaining equipment—it’s about protecting your bottom line and ensuring seamless operations. For even more information on the importance of PMs, you can find a collection of resources regarding best practices at: https://betterbuildingssolutioncenter.energy.gov/solutions-at-a-glance/preventative-maintenance-commercial-hvac-equipment
What preventative maintenance strategies have worked best for your business? Have you faced unexpected HVAC failures due to skipped PMs? How has regular maintenance impacted your operational costs and efficiency? Drop a comment below and share your experiences! Let’s start a conversation and learn from each other.

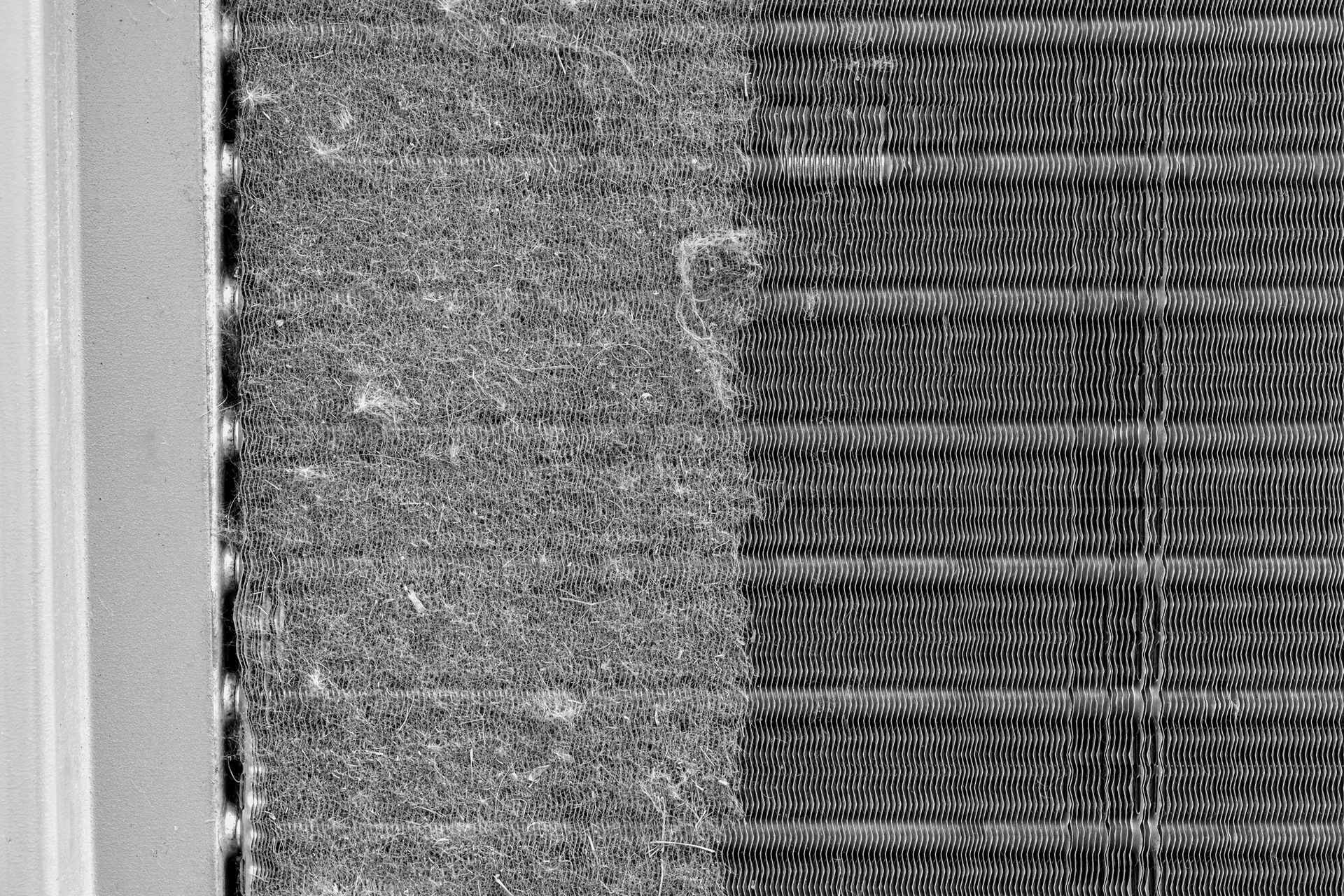
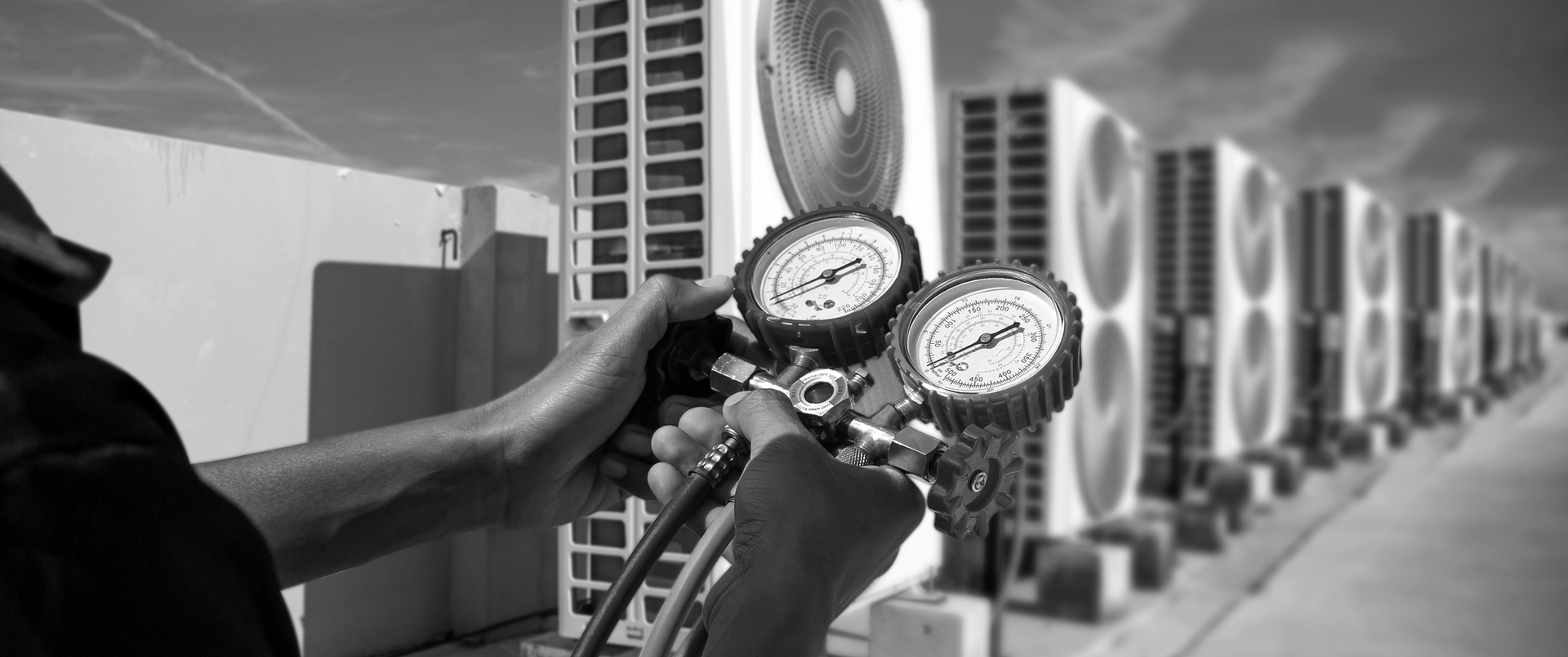